Distillery Planning Series: Batch vs. Continuous
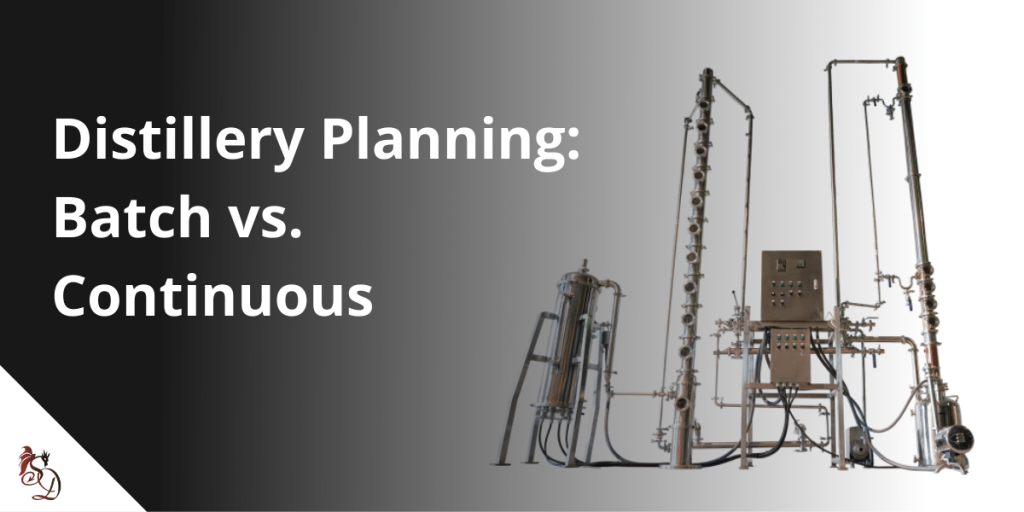
Batch distilling has been around for thousands of years, and somehow there’s always something new to learn about the process and how it all works. Distillation itself is a commonly used process in various industries to separate and purify liquids based on their boiling points. It involves heating a liquid mixture to its boiling point and collecting the condensed vapor.
There are two types of distillation processes: batch distillation and continuous distillation. Continuous distillation processes are the next step in the evolution of distilling, and even though the technology was developed in the early 1800s, they’re still at the cutting edge of distilling technology. They operate on a continuous feed of wort, and as long as all goes well, they do not need to shut down once they start up aside from scheduled maintenance. The two different technologies operate using the same basic principles, but since the technologies work differently, they each have their own unique strengths.
Batch distillation is a process in which a fixed amount (a batch) of a mixture is heated in a still until it reaches its boiling point, and the resulting vapor is collected and condensed into a liquid form. For simple batch distillation, this means that you’ll either need to do multiple runs or use a column with multiple plate levels to make a more refined product.
One advantage of batch distillation is that it is relatively simple and easy to operate. This makes it suitable for small-scale operations or new start-ups. It allows for better control over the separation of components to potentially allow you to pull unique flavors into your final product. However, batch distillation can be time-consuming and inefficient for large-scale operations, as the process needs to be repeated several times to obtain the desired amount of product. Furthermore, batch distillation may result in variations in the quality of the final product since it can be difficult to control all the variables from batch to batch.
Continuous distillation, on the other hand, is a process in which a liquid mixture is continuously fed into a column, where it is heated and vaporized. The vapor rises through the column, and as it does so, the lighter boiling constituents (heads) will move up the column, and the higher boiling point constituents remain in the liquid bed on the plate. The condensed liquid is then collected from one of the plate levels in our system as a final product. This contrasts the batch system, where the product normally leaves the column as a vapor before being turned into a liquid at the final product condenser.
An advantage of continuous distillation is that it can handle large volumes of liquid more efficiently than batch distillation. It is also more consistent, as the process is not interrupted, and the temperature and pressure inside the column can be carefully controlled. This leads to a more consistent and higher-quality final product. However, continuous distillation can be more complex and requires more expertise to operate and maintain.
The choice between batch and continuous distillation depends on what you want your operation to be. You’ll want to think about the amount of product needed, the quality requirements, the desired level of automation, and the final flavor that you’re trying to achieve. Batch distillation is a good choice for small-scale operations or any operation that needs to have a.
It is also a good option for processes that require a high level of variability or product mixes since it has such a wide operating range. Continuous systems excel at producing large volumes of distillate in a very consistent way. Automation can help reduce the learning curve for a continuous still dramatically, but there is inherently more complexity in the system, so there’s a lot to learn.
Batch distillation and continuous distillation are two commonly used distillation processes with different advantages and disadvantages. While batch distillation is simple and offers better control over the separation of components, it can be time-consuming and less efficient for large-scale operations.
Continuous distillation, on the other hand, offers higher efficiency, consistency, and quality control, but it requires more expertise to operate and maintain. Ultimately, the choice between the two depends on the specific needs of your operation, and we’d be more than happy to answer your questions and discuss your options. Call us at 561-845-8009 or leave a comment below to discuss your next still.