Liquid Transfer Pumps in the Distillery
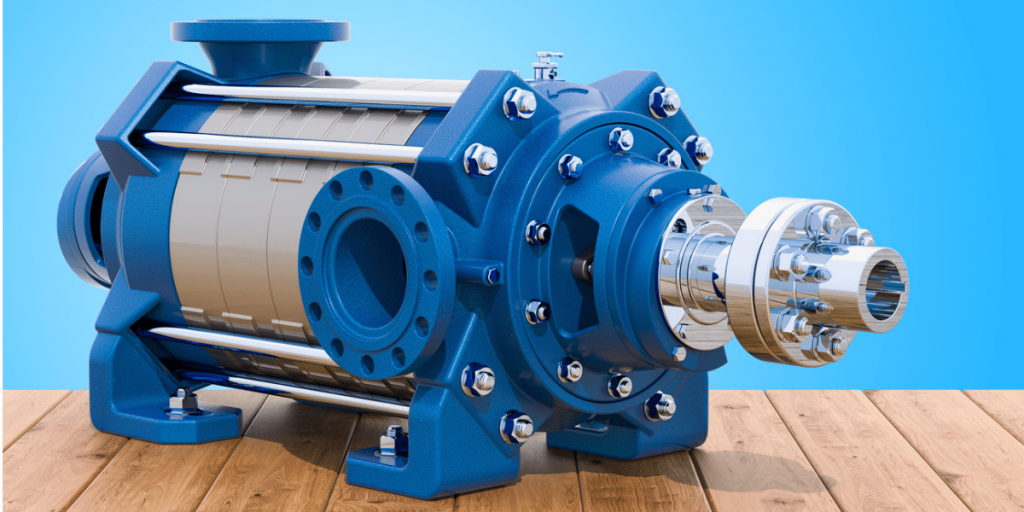
First let’s start here.
What Is Viscous Liquid?
A viscous liquid is defined as: Having a thick, sticky consistency between solid and liquid; having a high viscosity.
Viscosity is defined as: the measurement of a liquid’s resistance to flow, also referred to as a liquid’s internal friction.
Temperature of the viscous liquid can also affect viscosity. Cooler ambient temps usually mean that a viscous liquid can have an even heavier degree of viscosity. Therefore, hotter ambient temps will result in a thinner degree of viscosity.
Within the context of pumps in the distillery environment, the first thing that comes to mind when I think of a viscous liquid is molasses.
Several metrics can be used to measure the viscosity of liquids. Just to help give you a point of reference, here is a table below that illustrates how viscosity measurements are applied when using centipoise as the metric.

Unfortunately, the table above does not illustrate the viscosity of a typical grain in fermentation of bourbon for example. But we can make an assumption that a grain in bourbon beer has the viscosity of about 6000 to 8000 centipoise.
Ok so now let’s talk about types of pumps in the distillery and the best use for each type.
Let’s start with an industry work horse, the centrifugal pump. Centrifugal pumps work by pressurized fluid being introduced into an impeller housing where a rotating impeller with contoured blades then drives the liquid further downstream. As mentioned, the liquid needs to be under pressure when entering the impeller housing in order for this pump to perform well. This pump is not self-priming. To an extent this pump does handle grain in solids but can experience interruptions in flow if the material being pumped is too viscus. This is likely the most affordable type of transfer pump found in a commercial distillery and transfers low viscosity liquids very rapidly.
Next choice is the positive displacement pump category. There are several types of pumps to choose from here. The difference between centrifugal pumps vs positive displacement pumps is that with a centrifugal the liquid is essentially entering into the impeller housing under pressure whereas the positive displacement pump is self-priming and therefore can suck in material not under back pressure and can even have improved flow rates with more viscus fluids.
Flexible impeller pumps are a very common positive displacement pump in the distillery environment.
Flexible impeller pumps have a rubber cog with flexible vanes that press and bend against part of the inlet housing wall. The flexible vanes create a seal against the housing wall. This essentially traps fluids between the vane and housing wall in order to move fluids along as the impeller head spins. The downside to this is that the impeller head has a more limited-service life. So, a spare impeller head should definitely be kept available on the bench if this pump is your primary work horse.
Another popular positive displacement pump found in the distillery for viscus liquids is the lobe pump. Lobe pumps are very similar to gear pumps except the tolerances between each lobe is greater than the gear pump. This allows for larger solids to be pumped without damaging the pump. Suction ability is not as good as the flexible impeller and pumps slower. But far more capable of coping with heavy, viscus liquids day in and day out.
And finally on our list of pumps for the distillery environment is the gear pump.
Gear pumps are particularly good at pumping molasses, the most common ingredient used for rum production. Gear pump tolerances are typically closer than lobe pumps. External gear pumps operate by using the combined rotating action of two cogs positioned side by side within the housing. Internal Gear pumps operate by two interlocking gears of a different size with one rotating inside of the other.
Gear pumps are very reliable since they have minimal moving parts. Internal gear pumps can be used to load and unload.
Commercial distilleries very often utilize more than one type of pump in order to transfer fluids with varying degrees of viscosity efficiently. And finally, for the sake of redundancy, having a back up pump on the floor is always a good idea in case of a pump failure.