Where to Pack Your Vodka Still Column
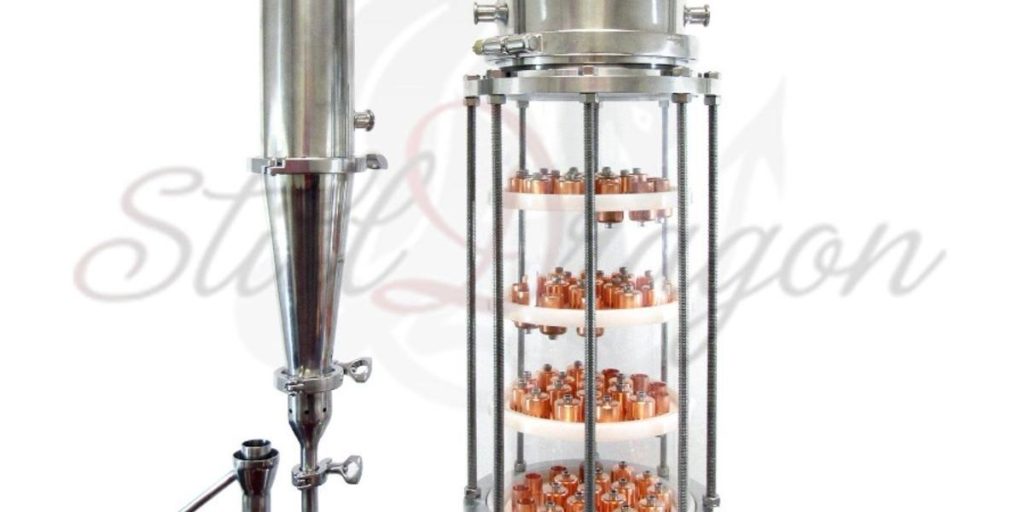
By: Larry Taylor
On more than one occasion I have been asked about mixing different distillation mediums. Whether or not to install packing material (random or otherwise) above or below the actual plate sections in your vodka still column?
This type of hybrid solution can help a small startup distillery save money on equipment and save valuable ceiling height typically preferred to run a “proper” vodka still column. It goes without saying, however, that it is ultimately up to the distiller to decide if the ethanol molecules have been sufficiently scrubbed enough to render the finished product clean enough to be considered “proper vodka.” Therefore, requisite plate (theoretical or actual) count is subjective.
Frankly, you can probably make the apparatus perform in any configuration. But you’ll get more optimal behavior with the packed section installed above the actual plate assemblies. And by that, I mean that actual plates (deeper liquid bed) will promote a sturdier temp gradient (compared to theoretical plates) that will be less affected by what will become unneeded heat emanating from the kettle.
In other words, the amount of heat needed in the kettle ultimately becomes unneeded in an optimally enriched still column – particularly at the top of the apparatus, where product is drawn off.
First, as a preface, check out a distillation temperature and concentration relationship chart for some background on the relationship of temperatures for liquid alcohol mixture / alcohol vapor temperatures.
Next, let’s dig into the distillation theory:
- It will require more heat to render alcohol from an 8% kettle charge than from a 15% or 20% charge. Therefore, the kettle requires at least twice (notwithstanding heat losses) the heat to render alcohol compared to heat needed at any of the plate levels. But the heat generated at the kettle has to go somewhere – usually straight up the still column to impact the temperature gradient. That’s an important point.
- Actual plates generally have a more abundant accumulation of liquid in a more confined place. So, one would say that plates maintain a dense liquid bed. The liquid that accumulates in packing (random or structured) is more or less in the form of accumulated droplets. Thus, the plates have a more dense accumulation of liquid in a smaller amount of area.
- The very first job or task of the liquid bed is to condense incoming vapor. And the deeper the liquid bed, the more capacity it has to absorb heat. So, this liquid on the plate is a cooling medium. And since this cooling medium is made up of a mixture of alcohol and water, it will be the percentage of alcohol on the plate that determines at what temperature vapor will flash and how much heat at that point is permitted to rise up to the next plate level. Therefore, the % of alcohol on the plate determines (self regulates) the temperature needed to allow further vaporization. In other words, a deeper liquid bed absorbs heat better, while the ABV on the plate determines the forthcoming flash point. Liquid droplets in packing have less ability to absorb what will become unneeded heat. Unneeded heat allowed to migrate up the still column shrinks the gradient and permits more water infiltration further up the column. That makes for lower ABV.
- The deeper liquid bed helps create a sturdier temperature gradient and relieves the burden off the packing to manage unneeded heat. This will allow cooler temperatures (higher ABV) to migrate farther down the column. This behavior acts to more completely enrich the packed still column and allow it to otherwise run faster without compromising the ABV.
I hope I explained the distillation theory with some measure of clarity. To summarize:
- Shifting as much alcohol as possible from the kettle into the still column will promote a more optimal temperature gradient. Fixed (bubble cap) plates will literally hold up liquid without regard to pressure. Packing must rely on pressure for liquid hold up. So, even though packing facilitates more potential distillation cycles (good behavior), the lack of liquid mass allows for more heat intrusion closer to the top of the apparatus (bad behavior).
- Minimize previously distilled alcohol from returning to the boiler too quickly.
- Utilize the larger liquid bed as a heat exchanger / buffer zone to minimize heat intrusion into the top of the apparatus.
For more practical tips and advice like this, stay tuned to the StillDragon distilling blog and be sure to check out our online forum.