Why Is Redundancy Important for Distilleries?
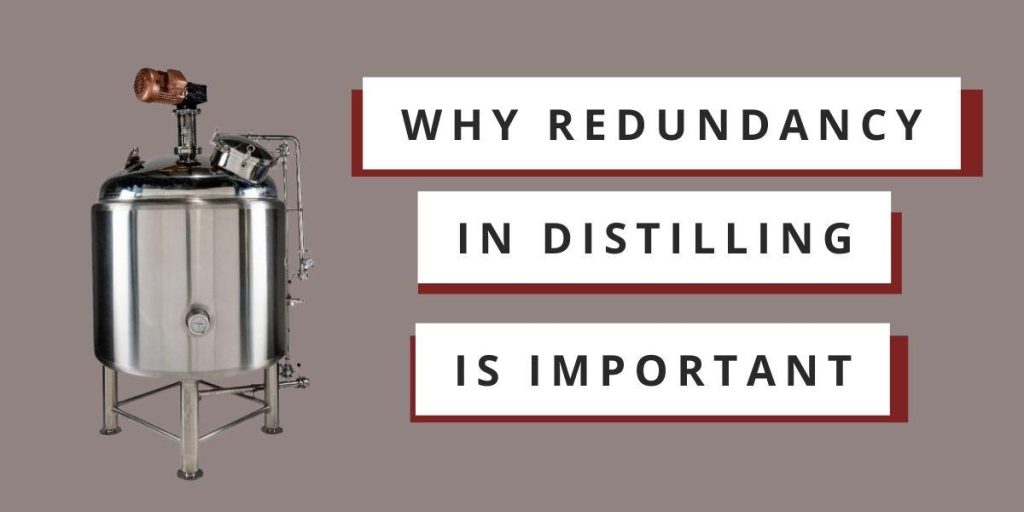
Picture it: you’ve spent 2 weeks fermenting for a large whiskey production order, you’ve got your staff ready to start charging your kettle, when suddenly your pump seizes, now you have no way to get the rest of your ferment into your kettle. It’s at this point that you start wishing you had a second pump just for backup.
That backup pump is a form of redundancy that every distillery should practice! Redundancy is the practice of having equipment on hand that doesn’t have a particular use at the moment, but it could become useful if other distilling equipment fails. It’s like having a generator in case the power goes out during a storm.
Benefits of Redundant Distilling Equipment
As you’re developing your budget for equipment, it is a best practice to factor in additional costs for the smaller things such as pumps, hoses, clamps, and gaskets. Adding in these extra costs, and the extra distilling equipment to keep on hand in case of emergencies is also a great way to ensure that you are not wasting money on labor or downtime in the future.
If a pump goes down in the middle of the run, you have to spend time trying to move your ferment into your kettle; depending on the size of your equipment, manually transferring could take serious dollars in terms of hourly wages for your staff.
Having even the small things on hand such as gaskets and clamps is helpful – you don’t want to be cleaning your equipment and accidentally wash a gasket down the drain, just to have to wait a couple of days to get a replacement. It could potentially put you days behind in your production schedule.
Having redundant equipment goes beyond just your basic distilling equipment. If you have a forklift to move equipment or barrels around the distillery, you would also want to have a pallet jack that is capable of moving the same weight, just in case something happens in the middle of operations but you are unable to get a forklift tech out for a few days. The pallet jack will at least keep you moving for the time being.
The most expensive part of distillery operations is the labor, not having redundancy in your distillery can cause your labor rate to quickly eat into your profit margins. If you have to cut hours because the equipment is down, this can also produce low morale amongst your staff.
Try setting up a redundancy cart. Grab a low-cost rolling toolbox and stock it with a few tools that are needed such as a screwdriver, crescent wrench, spanner wrench, and the basics for tightening equipment. Add a few extra clamps, gaskets, and assorted parts that might increase efficiency either when assembling, cleaning, or just doing regular maintenance. The toolbox can be rolled to where the work is being done and decrease the need to run back and forth to the supply room.
Developing a good maintenance procedure is another form of redundancy that can alleviate downtime due to equipment malfunction. Making sure that the equipment is in good working order when it is needed helps increase efficiency as well because it reduces the probability of needing to repair or replace equipment.
If you’re delegating money in your budget, but are wary about adding the extra pump or hoses, add up what the labor cost would be if your equipment goes down. It won’t take much to realize that redundant distilling equipment is less expensive in the long run. If you have any questions about what spare parts you should carry, give us a call at 561-845-8009 and we’d be happy to help you build a redundancy budget!