Why Insulate Your Column Still?
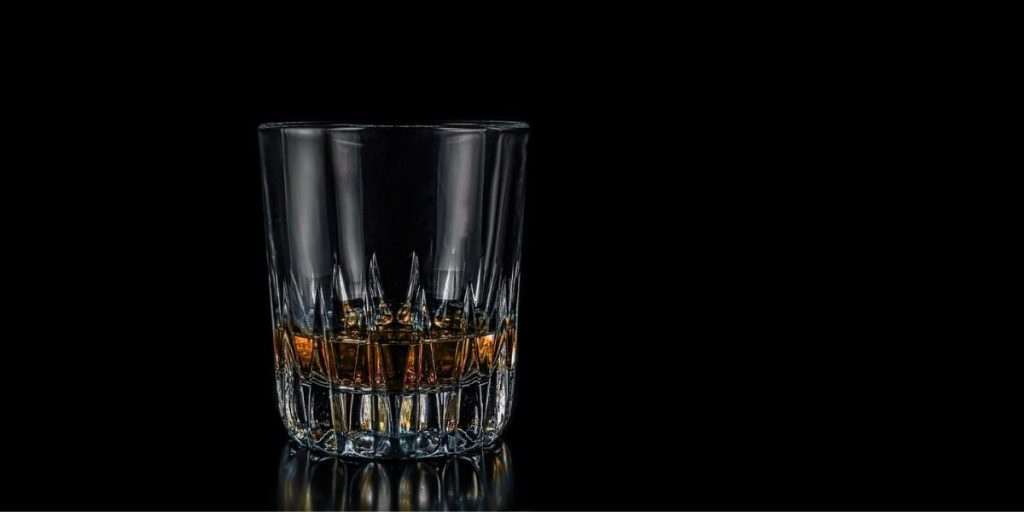
Photo by Michael Schwarzenberger
Distillation has been around for a very long time and, like most endeavors with that much history, the process can become as complicated as you want it to be. That much history leads to varying opinions on seemingly simple topics, and we’ll explore one of those in this article. Insulation is an often-overlooked option when you’re putting together a still, but it is something that you may want to consider adding to your reflux column design. Yes, you read that correctly. You may want to consider insulating a column in a reflux still.
Jacketed kettles often come with insulation, and that helps keep heat in the system and lower the overall energy input. This makes intuitive sense, as you’re throwing energy into the system to generate vapor. That energy will go wherever it can: metal is a good conductor, so the energy can escape through the kettle walls fairly easily. Single-walled kettles typically don’t come with insulation, so if you have one, it may be worth doing a cost/benefit analysis to see if your energy savings justify the expenses in a reasonable payback period. Less heat loss means less energy needed and faster heat-up times, so it can help you save valuable time and money.
When Not to Insulate Your Column Still
Insulating a column is similar in principle, but it’s done for different reasons. Plus, the type of column you’re running makes a difference. Columns that don’t have a dephlegmator will actually see a decrease in efficiency from insulation. While pot stills can achieve energy savings from insulation, columns that rely on passive reflux alone will be less efficient. This is because you need a temperature gradient to drive the passive reflux in the column.
When to Insulate Your Column Still
Insulation really shines in reflux column design when active reflux from a dephlegmator forces material back down the column. Insulating the column makes it easier to maintain equilibrium, giving a more consistent and higher quality product and helps maintain good column behavior, and aids in separation. By widening the operating range, it can also help the still run faster without sacrificing quality. Insulation also makes the still less susceptible to variations in the outside environment which further increases consistency.
Insulating Still Parts
Ok. Enough about insulating a column in a reflux still. What about insulating the other parts of the still? This one’s a little tricky since different parts of the still work differently than the kettle and dephlegmator. The way a dephlegmator works is by cooling the rising vapor and putting the less volatile components back into a liquid phase. Because the heat transfer is mostly happening inside the system adding insulation could be a two edged sword. If you’re running the cooling liquid through slowly, and the dephlegmaor is hot to the touch, then insulation hinders the cooling of the vapor phase. Insulating the lyne arm or the product condenser is not a good idea for similar reasons to the dephlegmator. You want some heat to escape off the lyne arm to help your product condenser cool the vapor to liquid more efficiently. The product condenser operates on the same principle as the dephlegmator, so it’s not a clear-cut answer.
To summarize whether you should add insulation to your reflux still design, it makes a lot of sense in the areas of your still where you’re actively heating (like the kettle) or if you’re trying to achieve equilibrium in a column with forced reflux. Non-reflux columns will see a negative return on the investment and the other parts of your still may or may not benefit from insulation.
Hopefully this information helps. If you have any questions, please feel free to give the team at StillDragon a call!