Distillation Columns: Packed Column vs. Trays
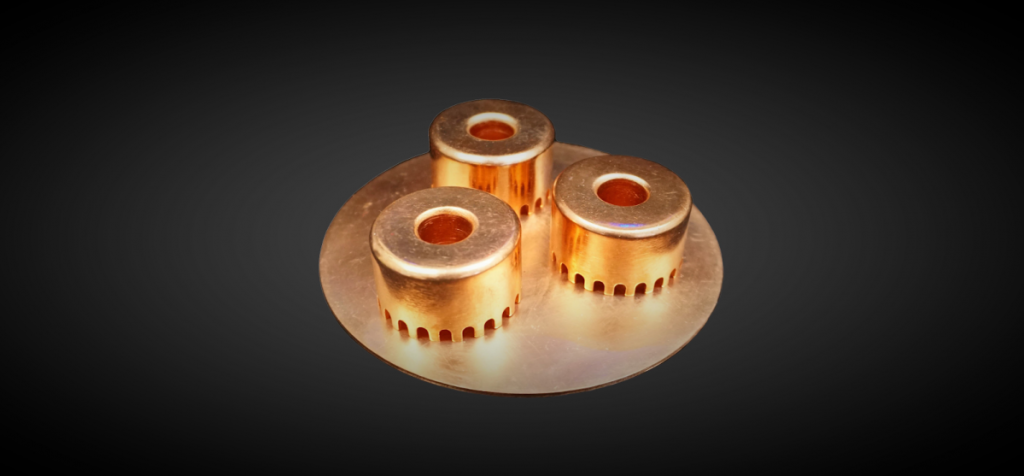
Let’s start this discussion by revisiting a bit of high school physics to ensure you are up to speed on distillation columns… First off, what is distillation? At its essence, it is evaporation. It is a phase change. Meaning that the liquid within the distillation kettle is brought to a boil until vapor is formed. (BTW, we see other examples of phase change when water freezes and becomes ice, a solid).
Distillation Columns 101
Once the vapor is formed in the distillation column, it will be driven toward the system’s discharge outlet by pressure within the system. This pressure is created by the generation of heat needed to boil the alcoholic solution in our kettle. This is an example of mass transfer. Therefore, we first have phase change, and then mass transfer. Ok, are we up to speed yet on distillation columns? Yes? Good.
So, if we can force the above-mentioned behavior within the distillation apparatus to repeat these processes multiple times while also provoking mass transfer, we can create multiple distillation cycles on the same constituents traversing through the distillation apparatus. Simply put, every time we create a full phase change cycle, our distilled solution becomes cleaner and the abv is boosted with each successive phase change cycle.
The modality we use to force this behavior to repeat is by using a literal tray (plate) to create a place for liquid to accumulate with each subsequent volley of mass transfer. Basically, the liquid boils, the vapor is formed, rises, gets directed onto a plate, the vapor condenses back to liquid on the plate, liquid reheats as entering vapor discharges its energy into the liquid. Then liquid re-heats till vapor is again formed, and the entire process repeats itself the next upward tray. Each tray acts like a wrung on a ladder so to speak.
Ok, so now that we have discussed that baseline information about phase change, mass transfer, and trays, we can now get into what kinds of trays are best for distilling for spirits production. There are many types of trays, but for our purposes, we’ll focus on the most common types of tray systems for distilling spirits.
The tray system with the widest operating range or “turndown ratio” really does do the best job of rendering a quality spirit as well as providing an optimal processing speed.
What Is Turndown Ratio?
A quick Google search will tell you that turndown (TD) ratio “refers to the width of the operational range of a device and is defined as the ratio of maximum capacity to minimum capacity. For example, a device with a maximum output of 10 units and a minimum output of 2 units has a turndown ratio of 5”.
There are many types of tray designs used in all manners of distillation. For spirits distillation, we will discuss the three most popular types of trays (i.e., sieve, valve, and bubble cap) and compare those against random packing material. Here is a tray comparison chart:
Sieve vs. Valve vs. Bubble Cap Trays
Sieve Trays | Valve Trays | Bubble Cap Trays | |
Relative Cost | 1.0 | 1.2 | 2.0 |
Pressure Drop | Lowest | Intermediate | Highest |
Efficiency | Lowest | Highest | Highest |
Vapor Capacity | Highest | Highest | Lowest |
Typical TD Ratio | 2 | 4 | 5 |
Operating Ranges of Structured and Random Packing Materials
In my mind, the most notable factor that favors tray use is that they can handle solids far better. Packing fouls easily. As a result, packing can be a real nuisance to clean and can become downright dangerous as seen at the Silver Trail distillery accident several years ago. Notwithstanding the potential for catastrophic fouling, cleaning a large-scale production system will also gobble up labor-hours.
The other equally important factor is the notion of maldistribution or an uneven distribution of the packing material within the column. Maldistribution contributes to enhanced sensitivity issues. In other words, it further reduces the operating range of the packing by not allowing for equal liquid and gas flow up and down the length of the column. It only takes a small bit of inconsistent loading in the packing into the column to create a problem such as channeling. Therefore, much greater care is needed when choosing and installing the packing material. Maldistribution is more problematic on the larger diameter column needed for legitimate commercial production volumes.
Packing can provide more theoretical trays and save valuable ceiling space. But with respect to more consistent still behavior and ongoing maintenance and durability, trays have the advantage.
Though many types of packing materials can be more affordable, trays provide a clear benefit within the context of distilled spirits. That’s not to say that a premium spirit can not be produced with a packed column, only that packing simply is not as user friendly as fixed trays.
> Got questions about commercial distilling equipment? We’ve got answers! Contact StillDragon today.